1.Select the material
The material can be roughly divided into three types: high-speed steel, cobalt-containing high-speed steel and solid carbide.
High Speed Steel (HSS):
Since 1910, high-speed steel has been used as a cutting tool for more than a century. It is currently the most widely used and cheapest material for cutting tools. High-speed steel drills can be used in both hand drills andamore stable environment such as a drilling machine. Another reason why high-speed steel lasts for a long time may be because high-speed steel cutting tools can be reground repeatedly. Due to its low price, it is not only used togrind drillbits, but also widely used in turning tools.
Cobalt-containing high-speed steel (HSSE):
Cobalt-containing high-speed steel has better hardness and red hardness than high-speed steel. The increase in hardness also improves its wear resistance, but at the same time sacrifices part of its toughness. The same as high-speed steel: they can be used to increase the number of times through grinding.
Carbide (CARBIDE):
Cementcarbide is a metal-based composite material. Among them, tungsten carbide is used as the matrix, and some other materials are used as binders to sinter by hot isostatic pressing and a series of complicated processes. Compared with high-speed steel in terms of hardness, red hardness and wear resistance, it has been greatly improved. But the cost of cemented carbide cutting tools is also much more expensive than high-speed steel. Cemented carbide has more advantages than previous tool materials in terms of tool life and processing speed. In the repeated grinding of tools, professional grinding tools are required
2.Select a coating
Coatings can be roughly divided into the following five types according to the scope of use:
Uncoated:
Uncoated tools are the cheapest and are usually used to process some soft materials such as aluminum alloy and low carbon steel
Black Oxide Coating:
Oxide coatings can provide better lubricity than uncoated tools, are also better in oxidation and heat resistance, and can increase service life by more than 50%.
Titanium nitride coating:
Titanium nitride is the most common coating material, and it is not suitable for materials with relatively high hardness and high processingtemperatures.
Titanium carbonitride coating:
Titanium carbonitride is developed from titanium nitride, has higher high temperature resistance and wear resistance, usually purple or blue. Used in the Haas workshop to machine workpieces made of cast iron.
Titanium Aluminum Nitride Coating:
Titanium aluminum nitride is more resistant to high temperatures than all the above coatings, so it can be used in higher cutting environments. For example, processing superalloys. It is also suitable for the processing of steel and stainless steel, but because it contains aluminum elements, chemical reactions will occur when processing aluminum, so avoid processing materials containing aluminum
In general, cobalt-containing diamonds with titanium carbonitride coatings or titanium nitride coatings are a more economical solution.
3. Choose the length.
The ratio of the length to the diameter is called the multiple diameter, and the smaller the multiple diameter, the better the rigidity. Choosing a drill with a blade length that is just right for chip removal and a short overhang length canimprove rigidityduring processing, thereby increasing the service life of the tool. Insufficient blade length is likely to damage the drill bit.
4. Select the drill point angle.
The 118° point angle is probably the most common in machining and is typically used for machining soft metals such as mild steel and aluminum. The design of this angle is usually notself-centered,which means that it is inevitable to machine the centering hole first. A drill point angle of 135° is usuallyself-centered,and since there is no need to machine a centering hole, this will make it unnecessary to drill the centering hole separately, thus saving a lot of time.
5. Select the helix angle.
A helix angle of 30° is a very good choice for most materials. However,inenvironments that require better chip evacuation and stronger cutting edges, drills with a smaller helix angle can be selected. For difficult-to-machine materials such as stainless steel, a design with a larger helix angle can be selected to transmit torque.
Production Process:
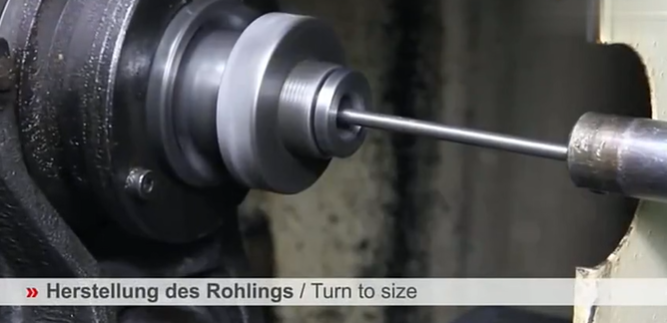
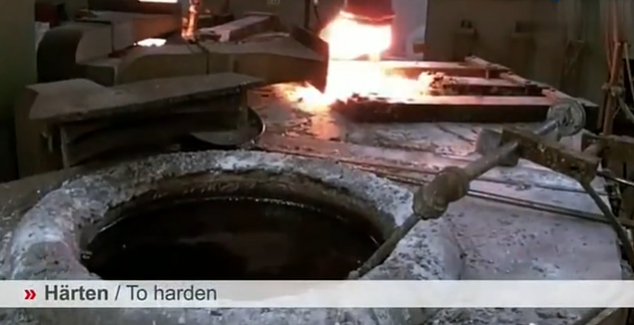
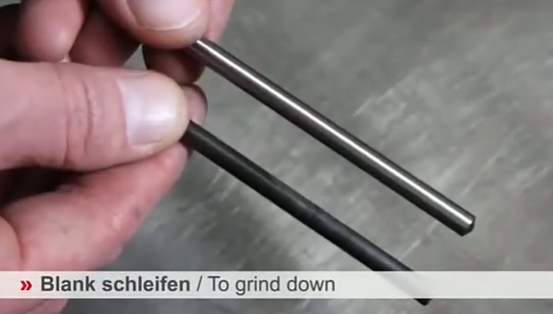
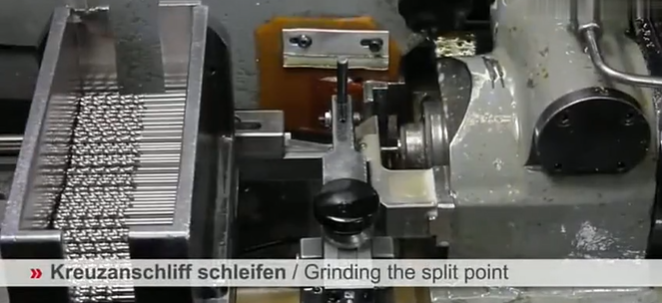
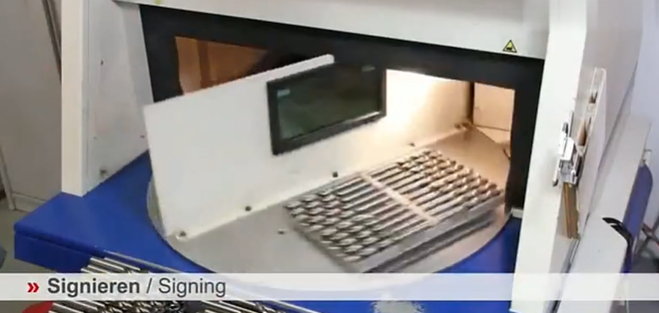
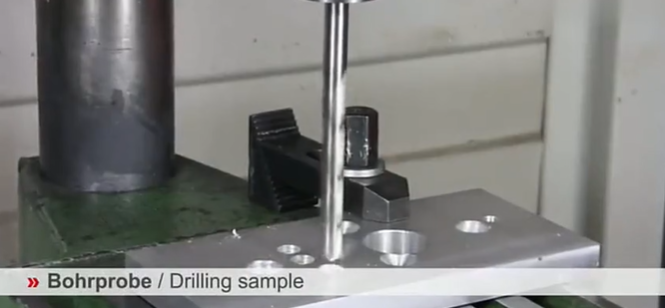